This is a Preprint and has not been peer reviewed. The published version of this Preprint is available: https://doi.org/10.1016/j.addma.2021.102061. This is version 4 of this Preprint.
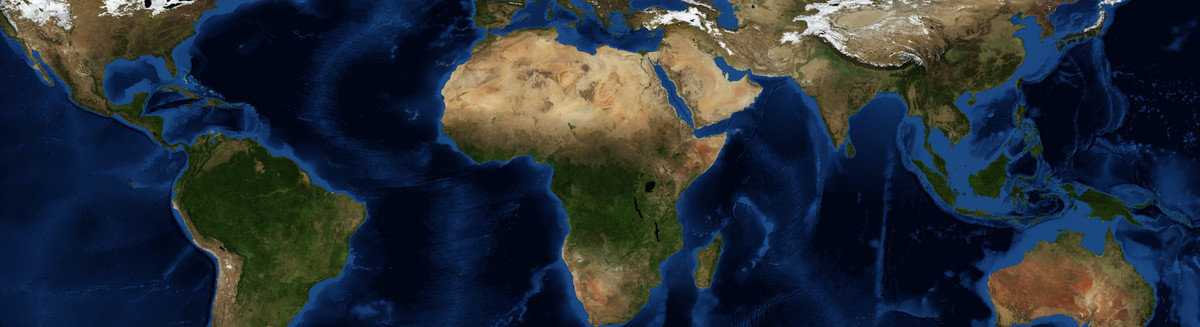
Predicting the yield stress of a 3D printed porous material from its internal structure
Downloads
Authors
Abstract
The design of any engineering structure requires the knowledge, and therefore determination, of the yield, i.e. limit of elasticity, for the building material. Whilst destructive experimental testing is currently necessary to do so, our work is part of initiatives which aim at deriving the yield without such laboratory experiments. The seminal work of Gurson (1977) on a simplified pore structure, a single spherical pore, first provided a theoretical relationship between the yield stress and the porosity. Specifically, it showed that the presence of pore space is responsible for the existence of a compression cap in plasticity, in addition to lowering the yield stress. This contribution extends the approach to determine the macroscopic yield of a porous material by taking explicitly into account its internal structure. As the yielding of a porous material is controlled by the geometry of its internal structure, we postulate that it is nearly independent of the constitutive plastic behaviour of the material. Here, we show that the influence of that internal structure on the yield could be retrieved from a finite element computation with just an elasto-plastic ideal material equivalent of the skeleton’s. With some basic knowledge about the skeleton’s mechanical properties, this process allows the determination of the yield stress without requiring the experimental compression of the material. We showcase the predictive power of the method against experimental testing, initially for a unique spherical void in a 3D-printed cylinder sample following Gurson, before demonstrating its applicability on a complex 3D-printed rock microstructure, reconstructed from segmented micro-Computerised Tomography scans.
DOI
https://doi.org/10.31223/osf.io/qfgz8
Subjects
Engineering, Materials Science and Engineering, Structural Materials
Keywords
3D printing, Internal structure, Yield stress
Dates
Published: 2020-05-12 17:40
Last Updated: 2023-08-30 15:52
There are no comments or no comments have been made public for this article.